

But after that, model and assemble the pickups, knobs and other hardware, build the depressions into the surface for them, and then “oh, let’s move those knobs around a bit, reposition the bridge…” It seems to me you’d really want to be in a history-based CAD software at that point, for experimenting with alternatives. So I look at that guitar and I think, Rhino would do a great job of making a nice complex curved surface for the body, which you could tweak endlessly with the control points. And anyway I’m on a Mac, so no plugins for me… There doesn’t seem to be any plugin that adds the kind of history-based rebuilding like above though. I haven’t been able to try it, but it looks kind of “klunky”, and is half the price again of Rhino.
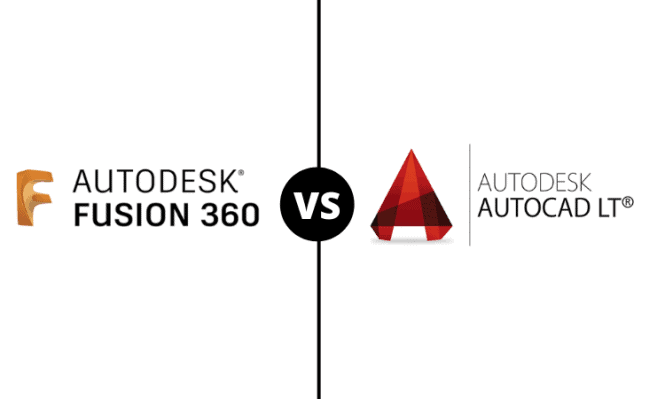
I guess that RhinoWorks could help with that. I know you can use layers to keep groups of objects separate, but it drove me crazy that things wouldn’t “stick together” the way I wanted when I moved them. In my first Rhino project, I had a frame made of aluminum profile, some curved sheets that attached to it in a certain way, and a bunch of hardware for the control panel. Then you can kind of slide things around, and have them stay attached in the way you expect. In Solidworks, Inventor, Fusion 360, etc., you can put objects into their own containers, and then connect them to other objects, specifying that certain points or surfaces should always stick together, holes should be concentric, and so on. I mean, it just can’t be done, as far as I can tell. Ok, so there are some cool things you can do in Rhino:īut in the end, the solution I found after an hour or so was:
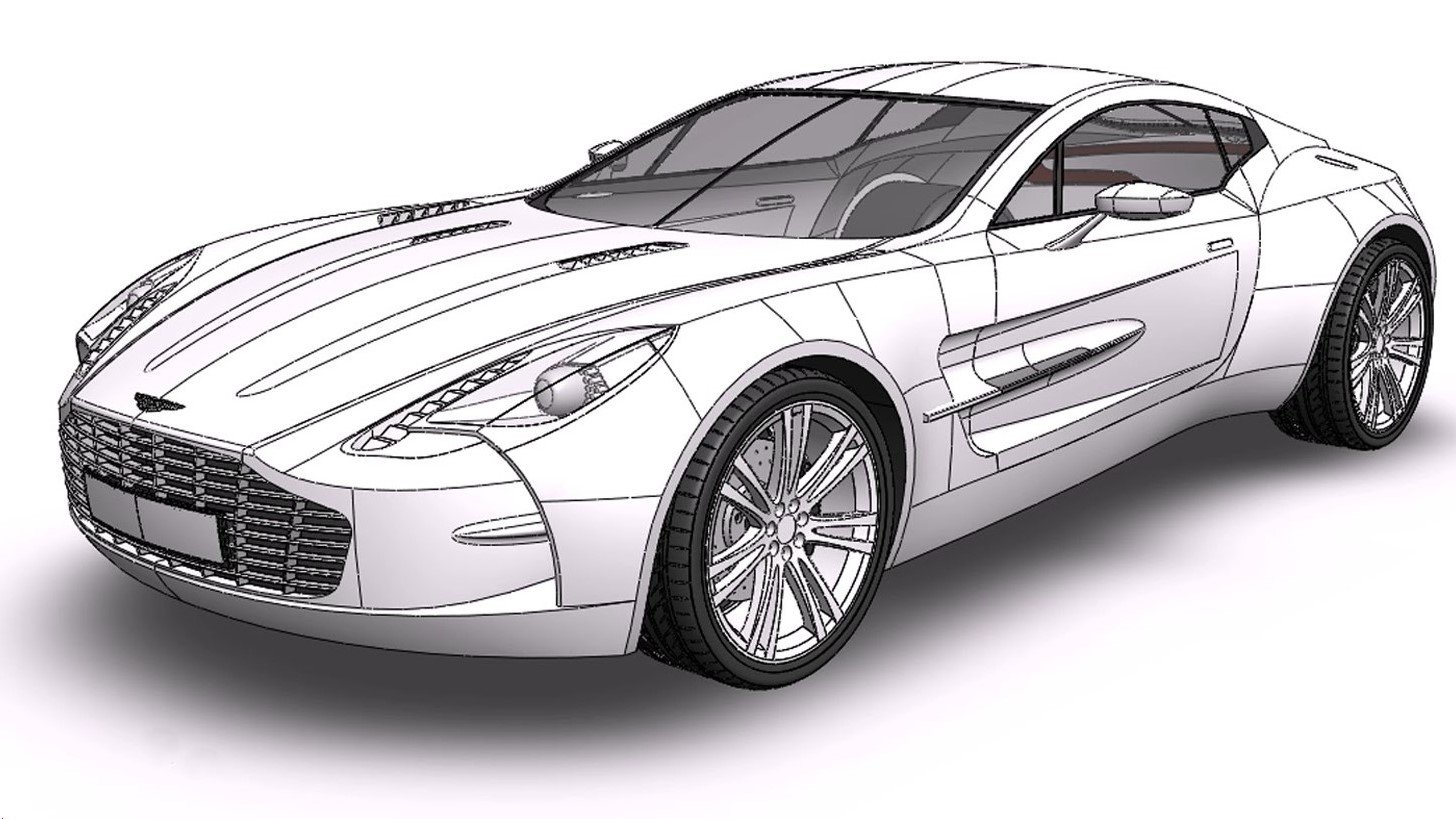
Then I went about trying to change the angle. Made with similar operations, except shell, because “polysurface is not closed”. So I double-clicked the draft operation in the timeline to edit it, and changed the angle from 9 to 12 degrees: Then I thought, actually, I want a bigger angle. I made a box, drafted the faces, split it, scaled up the top part, raised it, lofted between the top and bottom, put fillets on the edges, and shelled it. But anyway, to illustrate the point - I wanted to make this particular shape: There are a lot of things I don’t like about it - the whole “cloud app” thing for one, and also it’s buggy and sort of half-finished, and well, Autodesk. My experience so far has been a bit different, and the main cause of frustration - not being able to easily experiment with alternatives and make changes during the design process in Rhino. This definitely helps when a change is needed after the model is completed, but many designers like to experiment with alternatives and build ‘test geometry’ to see how it looks … which is not easy or what SolidWORKS was designed to do. As document management is built into the platform, files are automatically backed up to the cloud.Using parametrics (‘history-based’) every dimension is input at every step of the way. Fusion 360 includes integrated Assembly modelling, Motion studies, Rendering and FEA tools to help users analyse design before making it. In Fusion users can make drafts, prepare designs for 3D printing as prototypes or as final parts. It incorporates both direct and parametric control. Data management is built into Fusion.Īutodesk Fusion has a single model environment in which all unique parts and assemblies can be created.
Fusion 360 vs solidworks Pc#
As the app can run either on PC or on the cloud, it can work both with and without internet connection. It is a collaborative platform where users can access each other’s files which shortens design lifecycle. It is mostly used by students of manufacturing and design spheres.
Fusion 360 vs solidworks mac os#
Fusion 360 runs on Windows, Mac OS and in browsers. Solid, Surface, T-Spline and Mesh geometry are supported as well as drawing, rendering and 3D-printed output for design validation and documentation. Fusion 360 is a 3D CAD, CAM, CAE cloud-based platform by Autodesk, which connects the development processes of a product.
